What to Expect in an OSHA Inspection
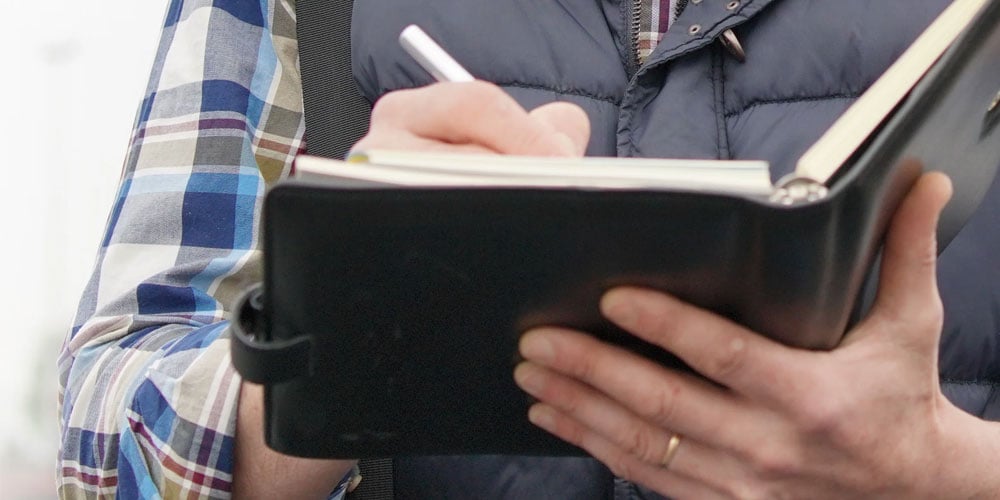
Whether you request an inspection by the Occupational Safety and Health Administration (OSHA) or they decide to conduct one on their own, it can be unsettling if you don’t know what to expect.
Each year, 2,200 OSHA inspectors visit 8 million jobsites to make sure employers are complying with regulations and working conditions are healthy and safe for more than 130 million workers. Here’s what you need to know to ensure the inspection at your place of business is a success.
How the OSHA inspection process works
Every OSHA inspection begins the same way: with the presentation of credentials. When the OSHA inspector shows up at your business, make sure to ask them for identification so you can verify that they are who they say they are.
It’s important to know that if you refuse entry to a verified OSHA inspector, you will be reported to the assistant area director for OSHA, who will obtain a warrant for entry. If you don’t cooperate with the inspection, OSHA may take legal action against your business.
Once you’ve checked the inspector’s credentials, you’ll sit down for an opening conference to discuss the purpose of the inspection and review any safety and health complaints they may have received about your business or through the workers’ compensation process. The conference may include both the employer and employees.
After this meeting, the inspector will walk around the facility and conduct the investigation. The inspection will end with a closing conference where the inspector will review the findings with the employer.
You can learn more about the OSHA inspection process in The OSHA Inspection: A Step-by-Step Guide.
What OSHA inspectors want to see
When the inspection begins, the inspector will ask to see many documents, including:
- A copy of your company’s written safety program
- Safety training records
- Medical surveillance records
- OSHA logs (if applicable)
- OSHA-required programs (if applicable)
It’s a good idea to have these items ready before the inspector arrives to help the inspection go smoothly.
After reviewing your records, the inspector will walk around your site to look for any unsafe conditions or practices, record notes about any OSHA violations they see, collect samples and take photos or videos. Along the way, they may mention any violations they see at your location. Be prepared that the inspector may also ask to interview employees to discuss possible compliance violations or complaints.
After the walkthrough, the inspector will share any violations they saw and abatement requirements with you during a closing conference.
When employers interfere
It’s important to make sure you’re not accidentally interfering with the inspection. For example, if you don’t let the inspector walk around, stop them from taking photos or videos, or keep them out of a certain area they’d like to inspect, you’re preventing them from completing the inspection properly.
Also, it’s considered interference if you don’t let them interview employees they’d like to talk to about health and safety at your location. If the inspector believes you are interfering, they may consider it a refusal. If this happens, they may end the inspection immediately and return with an inspection warrant.
Understanding citations and penalties
If an OSHA inspector finds a health and safety violation during an inspection, they may issue the employer a citation and a financial penalty. In general, OSHA must issue any citations within six months of the occurrence of any violations. OSHA will mail any citations to the employee representatives within a day of sending the citation to the employer. OSHA will also mail the citation directly to the employee, too, if preferred.
There are two types of penalty class – civil and criminal—and violations fall into four categories:
- General
- Serious
- Willful
- Repeat
If you are issued a penalty, be aware of the Federal Penalty Schedule:
- Serious violation - $975 up to $13,653
- Willful or repeat violation - $9,753 up to $136,532
- Failure to abate - Up to $13,653 per day beyond abatement date
If you have a repeated violation, OSHA may fine you even if they normally wouldn’t for the problem they spotted. If this happens, you might still receive a fine of hundreds to thousands of dollars.
To make sure you aren’t violating the rules, report the following to OSHA within 24 hours of the incident:
- Amputation
- Loss of an eye
- If one or more employees is sent to the hospital
Remember, in the tragic event that an employee is killed on the job, you must report it to OSHA within eight hours.
Getting ready
The best way to ensure a smooth OSHA inspection is to have strong health and safety programs in place to prevent injuries and workers’ compensation claims in the first place. This includes written plans for injury and illness-prevention programs, records of all the safety training you provide employees, a list of what measures you take to control hazards and comprehensive recordkeeping that can be reviewed at any time.
A successful injury and illness prevention program comes from the top down. Leaders should clearly communicate to employees that it is a top priority for the organization and play an active role in it alongside employees. The program should include standards for identifying and assessing hazards along with tips for preventing workplace dangers, too.
Training is an important part of any safety program. Make sure to providing injury and illness protection program training to all employees when the program is launched. Then be sure to train any new employees as they join the company.
All employees and leaders should have regular refresher training to make sure safety stays top of mind. Remember to evaluate your program regularly, too, and update it as needed. Since OSHA will request training records, be sure to document all training sessions and continued learning sessions so you can prove all employees have the information they need to work safely.
Employers are responsible for providing a safe workplace for employees that is free of hazards that may cause death or injury. CopperPoint’s Loss Control Toolbox, which has a resource material library, learning management system and videos available 24/7, can help you do just that.
When you make the effort to follow create a safe workplace that is OSHA compliant, you’re doing the best thing possible for your employees—and your business.
The information provided in this blog is intended for general information purposes only is not a substitute for review of current applicable government regulations, industry standards, or other standards specific to your business and/or activities and should not be construed as legal advice or opinion.